Extrusion equipment is mainly used for thermoplastic, plastic machine is one of the three categories (injection/extrusion/blow molding), occupies an extremely important position in plastic processing, can be used for forming pipe, bar, wire, plate, film, cable wire cladding and other various cross-section shapes of profile (such as plastic steel doors and Windows).
At present, there are generally three kinds of temperature control schemes for plastic extruders in China:
1. Discrete instrument (not recommended)
According to the requirements of processing technology, each area adopts temperature control meter + solid state relay (electric heating)+ solenoid valve (air cooling or water cooling). The effect of this control scheme is OK under static conditions, but the control under dynamic conditions (normal operation) can only be said to be mediocre even for air cooling, let alone water cooling equipment. Besides, the separate structure is not conducive to the implementation of heating current monitoring function (because each way requires a separate current transformer). In addition, the use of multiple temperature control meters. The whole circuit structure becomes complicated, installation, wiring and debugging are more troublesome, on the one hand, improve the labor cost, on the other hand, also increase the probability of failure.
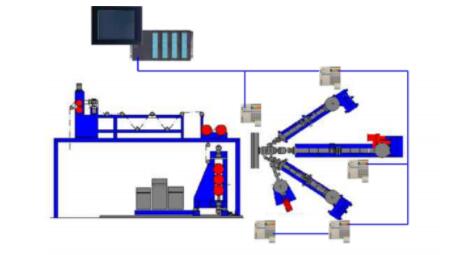
2, pure PLC control (not recommended)
The use of PLC built-in soft PID module to do temperature control, its integration exceeds the discrete instrument, the failure rate is low, but the technical level of personnel is higher, the field debugging is much more troublesome than a single table, and because of the PLC in floating point operation function on the limit, The actual control effect is even worse than that of a single table (because its PID function is very simple), and this scheme does not support the heating current monitoring function.
2, pure PLC control (not recommended)
The use of PLC built-in soft PID module to do temperature control, its integration exceeds the discrete instrument, the failure rate is low, but the technical level of personnel is higher, the field debugging is much more troublesome than a single table, and because of the PLC in floating point operation function on the limit, The actual control effect is even worse than that of a single table (because its PID function is very simple), and this scheme does not support the heating current monitoring function.